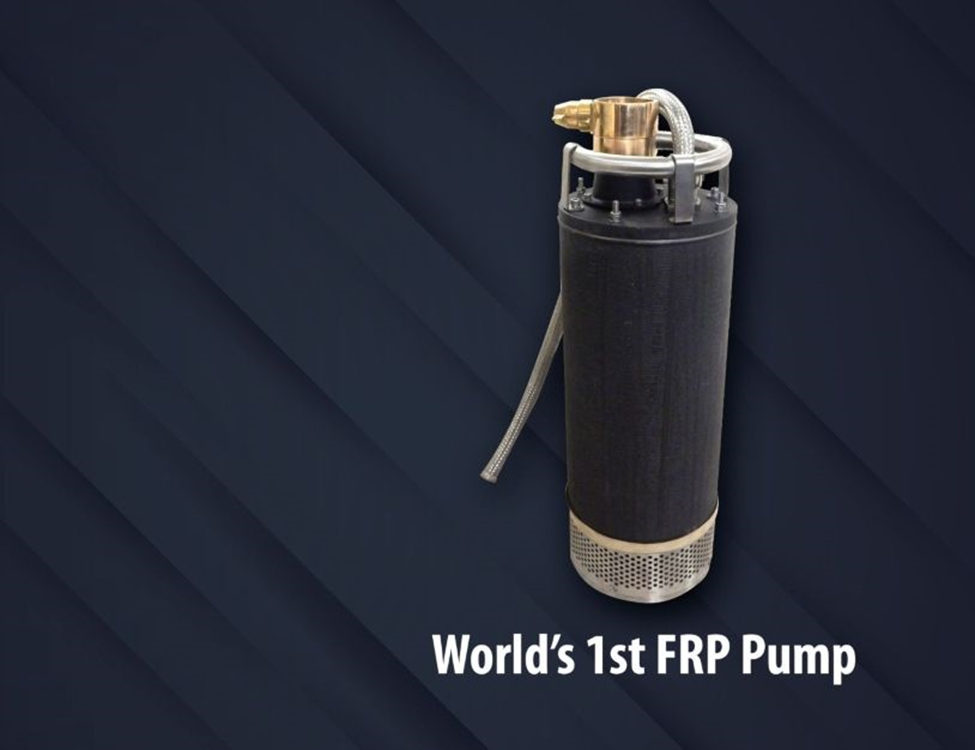
Dewatering pumps operate occasionally, but when used, they perform critical life-saving operations. They must be easy to carry & their parts should not deteriorate during long storage. We addressed these vital concerns by developing our dewatering pump using FRP composite material. Our 5 HP pump has the lowest weight in its class, which makes it man-portable. Being in FRP, the pump resists environmental degradation from weathering, corrosion & rot in the long term.
In the modern world, FRP products have found their way into all types of industries. Modern aircraft are made with up to 50% of their parts manufactured in FRP. In the automotive industry, vehicles are completely made of FRP parts. In the construction industry, structures are FRP retrofit. This increases its load-bearing capacity. In the marine industry, parts are susceptible to corrosion. Such parts are being replaced by FRP products. Fluid handling equipment is susceptible to corrosion. FRP products are corrosion-resistant, thereby increasing the life of such equipment. The major disadvantage of using FRP is their high initial costs. The manufacturing and testing process for FRP needs specialized infrastructure and investments.
Fibre-reinforced plastic (FRP) is a composite material. The material is made of polymer plastic, which is reinforced with fibres for strength. The fibre could be made of glass fibre, carbon, aramid, or basalt. FRP manufacturing involves two critical processes. The first process involves fibre manufacturing. The fibre performs are manufactured through weaving, braiding, stitching, and knitting. The second process involves bonding the fibre with the plastic polymer. The bonding process is done by many methods. The methods include compression moulding, bladder moulding, and wet layup. FRP material has many benefits compared to its metal counterparts. FRP materials are corrosion-free, oxidation-free, lightweight, and stronger than metal. FRP materials weigh 75% and 30% less than Steel and Aluminium.